A spunbond nonwoven machine is a piece of equipment used to manufacture nonwoven fabrics. Nonwoven fabrics are sheets or webs of fibers that are bonded together through various methods, without weaving or knitting. In the spunbond process, the fibers are extruded, drawn, and laid down on a conveyor belt to create a web, which is then bonded to form a fabric. Here is a general outline of the process:
Polymer preparation
The raw material, typically a thermoplastic polymer such as polypropylene or polyester, is prepared in the form of granules or pellets. These are fed into an extruder, where they are melted and homogenized.
Extrusion and fiber spinning
The molten polymer is forced through a spinneret, a device with numerous small holes that extrude the polymer into fine filaments. As the filaments exit the spinneret, they are cooled and solidified, typically using a stream of cold air.
Quenching
The cooling process solidifies the fibers, and they are stretched to reduce their diameter and increase their strength. This stretching process is known as drawing.
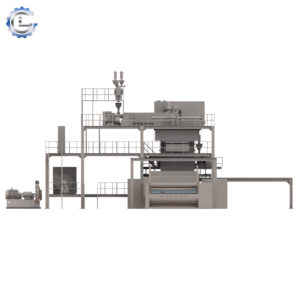
Laying down the web
The drawn fibers are collected on a moving conveyor belt, where they overlap and interlace to form a random web with a uniform thickness. The speed of the conveyor belt, the rate of extrusion, and the air flow all affect the web’s characteristics.
Bonding
To create a stable fabric, the fibers in the web must be bonded together. In the spunbond process, this is typically achieved through thermal bonding or calendering. The web is passed through heated rollers that apply pressure, causing the fibers to melt slightly and fuse together.
Finishing
After bonding, the fabric may be treated with various finishes to enhance its properties, such as water repellency, flame retardancy, or UV resistance. It may also be cut, slit, or combined with other materials to create the final product.
Winding and packaging
The finished fabric is wound onto rolls, which can then be shipped to customers or further processed into finished goods.